

“At the culmination of my thirteen years of playing organized football — at a time when a head injury cost me a quarter of my senior season — I came to the realization that there was a lack of awareness regarding the need for regular helmet maintenance.”

Football helmets provide the best protection when properly fitted to a player's head.
Helmetfit founder Mike Weatherby saw too many players taking the field with ill-fitting helmets and wanted to do something about it.
Proper fit involves inflating air bladders inside the helmet - via a series of inflation ports on the back of the helmet - each and every time a player takes the field. Typically this would be done by a coach or equipment manager using a hand-held bulb pump, working with the player and ensuring minimal play in all directions.
As you might suspect, this time-consuming process was happening only sporadically, with varying levels of expertise, and no accountability.
Weatherby came to us looking to develop a hand-held smart inflation system that would capture each player’s specific fit data. Once a proper fit was established for a player, the system would enable fast and precise fit maintenance to be performed each time a player took the field.
After interviewing coaches and equipment managers, we developed a variety of concepts which took into consideration size, portability, functionality, and ergonomics for both on- and off-field use. We landed on a design that clipped a smartphone to the device - similar to a spring-loaded car mount - that connected to the device via bluetooth. This approach had numerous advantages from a hardware and interface standpoint, as well as reducing overall cost.
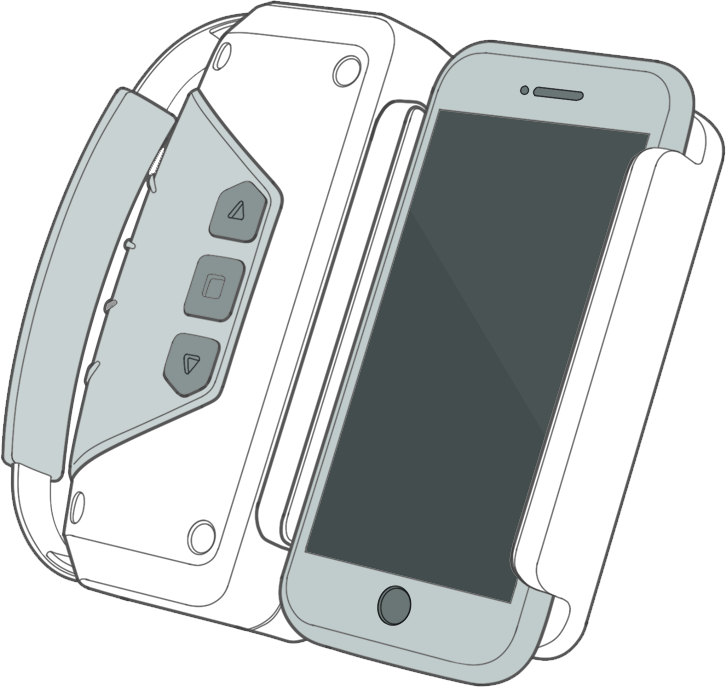
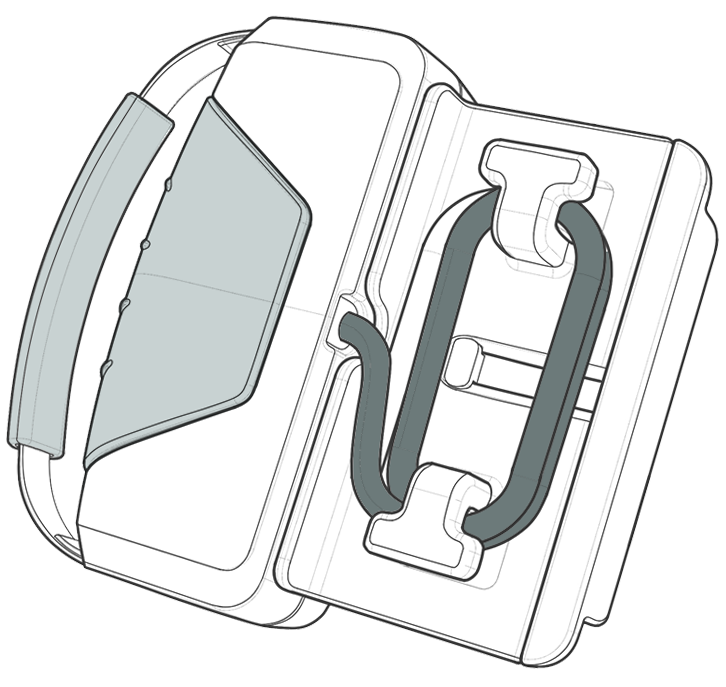
Next we identified the various user tasks, which fell into 2 distinct categories:
Administrative tasks - such as creating a team, adding players and helmet specifications, and configuring settings - could be performed independently from the pump.
Functional tasks - such as performing the initial fit or maintenance fits for a player - were device-dependent and had unique interaction requirements. For these, the tactile device buttons needed to allow users to navigate the interface and complete the tasks.
The former were typical mobile tasks with established patterns, most likely performed off-field. Functional tasks needed to be easily performed with one hand, leaving the other free to use the inflation needle and to physically check various aspects of the fit. The operator’s attention would also be split, as they worked with the player to ensure a comfortable fit.
We created typical user flows to flesh out the admin tasks. For the functional tasks, we created digital / physical workflows - a format of our own devising that maps physical and digital interactions in parallel - to ensure that the device and interface supported the unique physical and cognitive requirements of these tasks.
This led to the development of a hybrid interface - one that could be navigated via typical touch interactions or by using the directional keys on the device itself.
The Functional task flows guide the user through each step of the process, allowing them to continue by pressing the right arrow key, go back by pressing left, and to navigate lists or inflate / deflate by pressing the up or down keys. Arrow icons on the currently selected action reinforce this navigation throughout, as do screen transitions and animations.
We leveraged the accelerometer in the phone to reverse all directional pad controls when the device is inverted - allowing for intuitive use in either hand.
We presented the instructional graphics to match the physical orientation of the operator and player. Since the bladder ports are on the rear and top of the helmet, the operator typically stands behind the player. When we introduced the idea of an “off-player fit”- where bladders can be inflated without the player there using alternate PSI readings - we removed the player and displayed only the helmet. This visual mapping helps operators avoid mistakes without much thought.
From there, industrial design, electrical engineering, and mechanical engineering moved forward with the hardware prototype; and interaction design, electrical engineering, and the software development team moved forward with app development, prototyping, and user testing.
The engineering team sourced a pressure sensor that is extremely precise — down to +/-0.00023206038 psi — and that also measures air temperature to help compensate for the difference between outdoor temperature and player’s head temperature due to changes in volume based on the ideal gas law.
Validation testing with a simulated, 3D-printed prototype attached to an iPad mini provided valuable feedback about the directional keypad from a group of high school and college coaches.
Insights from this research led to the rejiggering of several features and addition of new ones, including a well to store a small amount of lubricant right in the pump. Precision inflation requires a lubricated needle, but many users either forget or ignore this step – having it handy might encourage people to do it. The needle clicks into an impression designed to hold it in place when the cord is wrapped – and the cord is designed to a specific length to help the user achieve this.

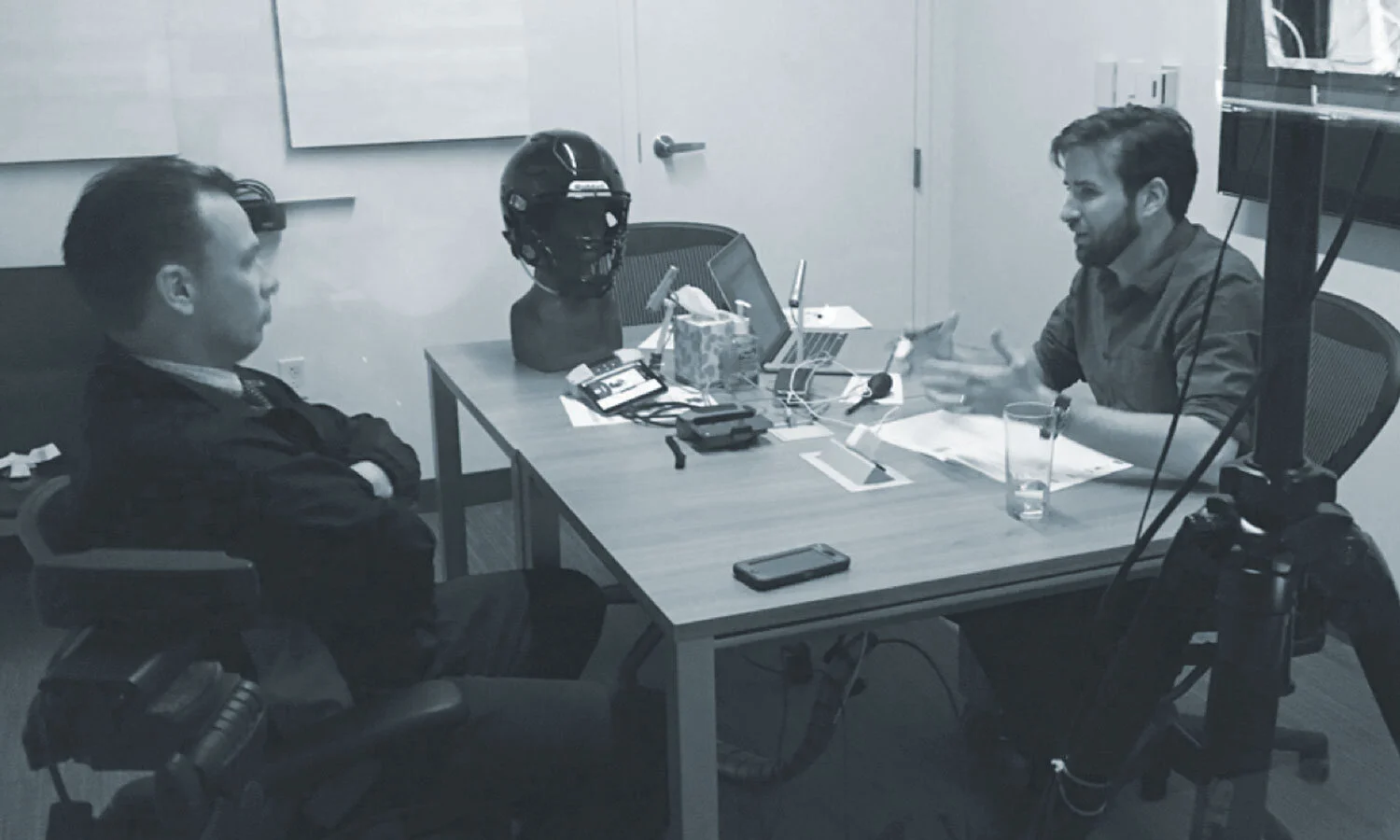
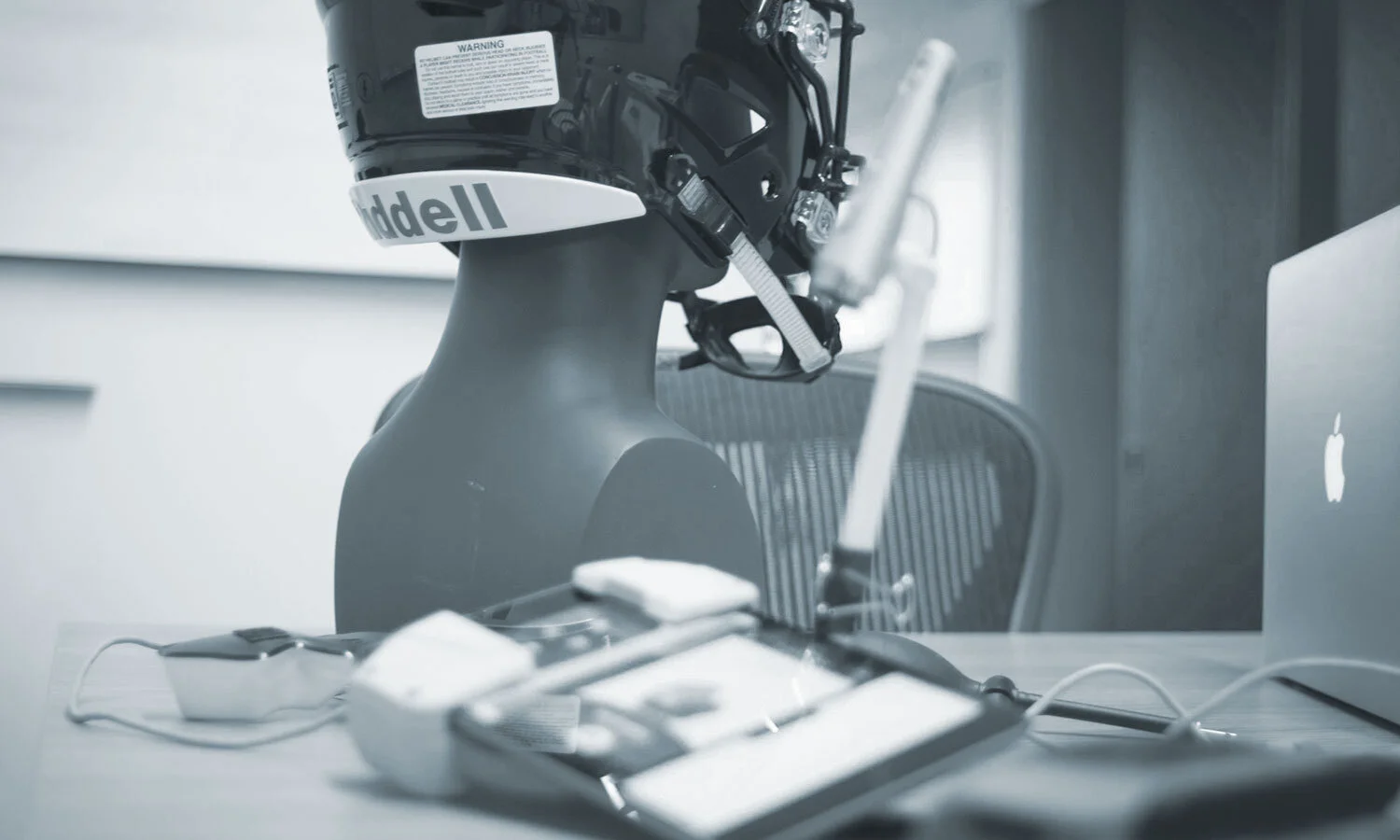
Helmetfit is now being used by a growing number of college and professional football teams.
“ I’ve been in this industry over 35 years, and I think this is something that’s long overdue. It’s a product that should be in every locker room.”
